I. Background Introduction
Gas chromatography technology was first introduced in the 1950s. It is a new separation and analysis technology. Based on the differences in the physical and chemical properties of the components, the difference in the boiling point, polarity, and adsorption properties of the substances is used to achieve the separation of the mixture. It is a major scientific and technological breakthrough and is widely used in many fields.
Petrochemical analysis industry: (1) analysis of crude oil; (2) analysis of oil products; (3) analysis of sulfur and nitrogen-containing compounds; (4) analysis of aliphatic hydrocarbons and aromatic hydrocarbons.
Environmental analysis: (1) Atmospheric pollution analysis (toxic and harmful gases, gas sulfides, nitrogen oxides, etc.); (2) Water resources (including organic pollutants in freshwater, seawater, and wastewater); (3) Soil analysis, etc. (Organic pollutants, solid particulate waste).
Food analysis industry: (1) Analysis of pesticide residues; (2) Analysis of food additives; (3) Analysis of volatiles in packaging materials, etc. Medical analysis: (1) Analysis of amino acid derivatives in blood; (2) Analysis of certain volatile drugs, etc.
II. Application Introduction
1. The principle of gas chromatography separation:
The difference in the boiling point, polarity and adsorption properties of the substance is used to separate the mixture. After the sample to be analyzed is vaporized in the vaporization chamber, it is carried into the chromatography column by an inert gas (ie, carrier gas, also called mobile phase). The column contains liquid or solid (Stationary phase). The boiling points, polarities, or adsorption properties of the components in the sample are different. Each component tends to form a distribution or adsorption equilibrium between the mobile phase and the stationary phase. Due to the flow of the carrier gas, the sample components are repeatedly distributed or adsorbed/desorbed during the movement. As a result, the component with the higher concentration in the carrier gas flows out of the column first, and the component with the higher concentration in the stationary phase is distributed. After the components flow out. When the components flow out of the column, they immediately enter the detector. The detector can convert the sample components into electrical signals, and the size of the electrical signals is proportional to the amount or concentration of the measured components. When these signals are amplified and recorded, it is a gas chromatogram.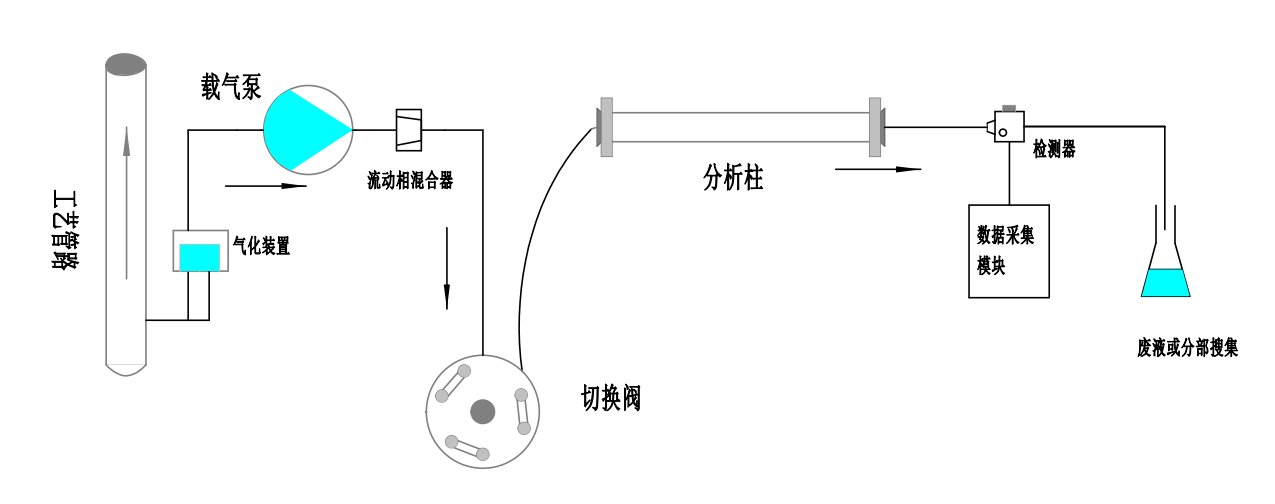
2. The main process of gas chromatography separation:
(1) Gas sampling system: use carrier gas to load the gas to be tested. The carrier gas is mostly inert gas, such as nitrogen, argon, helium, etc., which is loaded by the pump and outputs a stable pressure, driving the sample to flow in the chromatography column, and pushing the separated components into the detector.(2) Separation system: the sample to be analyzed is carried into the chromatography column by the carrier gas, and the column contains a liquid or solid stationary phase. Due to the different boiling points, polarities, and adsorption properties of the components in the sample, each component It tends to form a distribution or adsorption equilibrium between the mobile phase and the stationary phase. The component with a higher concentration in the carrier gas flows out of the chromatographic column first, and the component with a higher concentration in the stationary phase flows out after the component is separated. .
(3) Detection and recording system: The components flowing out of the chromatographic column enter the detector for detection. There are many types of detectors. Commonly used are hydrogen flame ionization detector (FID), thermal conductivity detector (TCD), and nitrogen and phosphorus detection. (NPD), flame photometric detector (FPD), electron capture detector (ECD) and other types, their structures and principles are different, there are those that use ionization out ion current detection, some that use component thermal conductivity difference detection, There are components that use combustion to emit light through wavelengths, so detecting different components requires different detectors.
III. Application difficulties
1. The output flow of the carrier gas pump needs to be stable to ensure a stable sample injection volume.2. The pump will bear greater pressure in the gas circuit, and it is necessary to ensure the stability of the pump and the consistency of the parameters under different pressure fluctuations.
3. Some detectors will radiate heat (such as FID) to the surroundings during operation, which is easy to form a higher temperature environment in a narrow space. It is required that the pump can work stably in a higher medium or ambient temperature.
IV. Solution
D35 Micro Diaphragm Compressor

1. Small size and stable flow rate, fiber reinforced nylon and EPDM rubber materials, with good resistance to corrosive media;
2. The parameter consistency is high, and it can work stably under harsh working conditions such as high temperature environment and high temperature gas transmission;
3. The use of interference-free brushless motor will not affect other interference-sensitive components of the equipment;
4. Both the suction port and the exhaust port of the air pump can carry a large load, without fear of pressure fluctuations caused by the front and rear processes of the equipment.